The science of moving a fluid from point A to point B is vast, and knowing when to use one type of pump or another often requires expert engineering assistance like the kind we provide at West View Cunningham. In this article, we discuss some basics of where and how to apply different technologies to help you start your search for the right pump and achieve best results from your pumping systems.
Positive Displacement Pump
Centrifugal Pump
Positive Displacement (PD) Pump Basics
_Page_1_Image_0001.png?width=179&name=Roper%20Pumps%20Line%20Card%20(July%202021%20Newsletter)_Page_1_Image_0001.png)
The main varieties of Positive Displacement pumps are:
- Gear
- Air-Operated Double Diaphragm (AODD)
- Diaphragm Metering
- Progressive Cavity (e.g., hose pumps, eccentric screw pumps)
- Piston
- Sliding Vane
Positive displacement pumps come in a wide variety of configurations. Each works in slightly different ways, but at their core they all make a fluid move by trapping a fixed amount of liquid and forcing (i.e., displacing) the trapped fluid into the discharge pipe. This type of actuation can be controlled precisely. As a result, the vast majority of metering pumps are of the positive displacement variety, the most common being electrically actuated diaphragm and hose pumps.
Gear pumps are designed to transfer higher viscosity fluids of >100cP at low to medium flow rates. They are most often used for bulk transfer applications between chemical processes/tanks moving heavy fluids like resins, paints, or tars. Gear pumps have poor solids handling capabilities, particularly if they are set up to run on thinner fluids with a tight gear mesh.
AODD pumps are unique because they are powered by compressible air or gas, so many of the considerations noted below are not a factor when using them. AODD pumps will never exceed the pressure ratings on their curves and are generally a 1:1 ratio of air supply pressure to maximum discharge pressure. If the system becomes pressurized to the limit of the pumps discharge pressure, it will simply stall until the system pressure drops again.
In this regard they are very forgiving in the field – no pressure relief is required and they can be dead headed or dry run almost indefinitely without failure. For this reason they make excellent filter-press pumps. AODD pumps can be used for almost any application and make excellent portable back-up pumps. They are not often considered as a first choice for permanent installation due to the cost of compressed air versus electricity.
Progressive cavity pumps, also known as progressing cavity, generally refer to the eccentric screw pump, though there are several pump types in this category. They are often used as a “pump of last resort.” They have middling performance characteristics and generally poor efficiencies, but those shortcomings are offset by their ability to pump nearly anything. This is particularly true of “fluids” that are otherwise not pumpable, such as spent grain at a brewery or whey powder and oil mixtures at a food processing plant. They require regular maintenance because the rotor and stator are both wear items and may require frequent replacement depending on the service.
Piston pumps are generally used in high-pressure injection or spraying applications, such as pressure washers for car washes or main pumps at small injection wells. They work best in low to medium flow applications, as scaling them up beyond a couple hundred gallons per minute becomes prohibitively expensive. Generally, that is a range where a multi-stage centrifugal pumps will be a more reliable option. Piston pumps have very strict requirements for inlet pressure and drive torque which must be catered to in the system design, otherwise, they have reliability problems. They also create rapid water hammer pulses in the discharge line, so pumping into a pressurized closed system is not recommended without adequate pulse dampening.
Sliding vane pumps are more specialized pieces of equipment, typically used on light hydrocarbon applications like propane transfer. They create excellent suction and require very little NPSHa to operate, so they are perfect for liquids with high vapor pressures. The vanes themselves are a regular maintenance item and require replacing on a schedule.
The benefits of using PD pumps include:
Flow directly proportional to speed & easily controllable
- Accurate & repeatable:
- Basic models are generally capable of flows of ±5% accuracy to set point
- Metering models can achieve flows of ±0.05% accuracy to set point
- Can achieve very high pressures (10,000+ psi)
- Flow & discharge pressures unaffected by system back pressure
- Higher efficiency with high-viscosity liquids vs centrifugals
Some engineering considerations/drawbacks when using Positive Displacement pumps are:
- Some form of pressure relief system is required on the discharge of the pump
- Any PD pump that uses linear motion to pump (e.g., AODD, Diaphragm, Piston) creates pressure pulses in the piping to which they are attached. This feature must be accounted for if the system pumps into a pressurized line or vessel.
- Most PDs require regular maintenance such as replacing diaphragms, stators, hoses, or vanes
- Most PDs have strict maximum inlet pressure requirements that cannot be exceeded
- PDs generally cap out at 500gpm max capacity, and the sizes of units that have higher capacities start to become prohibitive
- PD pumps are not additive for discharge pressure, and therefore not suited to pressure boosting applications.
- PD pumps, in general, CANNOT be run in series in a pipeline.
- AODDs, piston pumps, and some types of progressing cavity pumps CANNOT be run in parallel without causing severe damage to themselves and/or the system to which they are attached
An Overview of Centrifugal Pumps
Centrifugal pumps are the most common pumps in the world and can be found in an absolutely bewildering array of shapes, sizes, and configurations. Unlike PD pumps, which vary in pumping mechanism from type to type, all centrifugal pumps work exactly the same way. Centrifugal pumps transport fluids by creating a pressure differential inside the pump casing that induces a flow in the system. This movement is achieved by converting rotational mechanical energy through the impeller into pressure energy in the fluid.
The performance of a centrifugal pump, unlike that of PD pumps, is intrinsically tied to the system in which the pump is installed. Pumps must be properly sized and selected based on the system parameters to run in a stable hydraulic condition. The pressure differential created by the pump will only ever match the pressure required to induce a flow at a single point along the pump curve, as shown in the graphic below. Missing the mark in sizing and installing a pump into a system that isn’t capable of matching the curve will lead to myriad problems. We have several articles discussing these issues in detail, see our article on sizing and our article on system modeling.
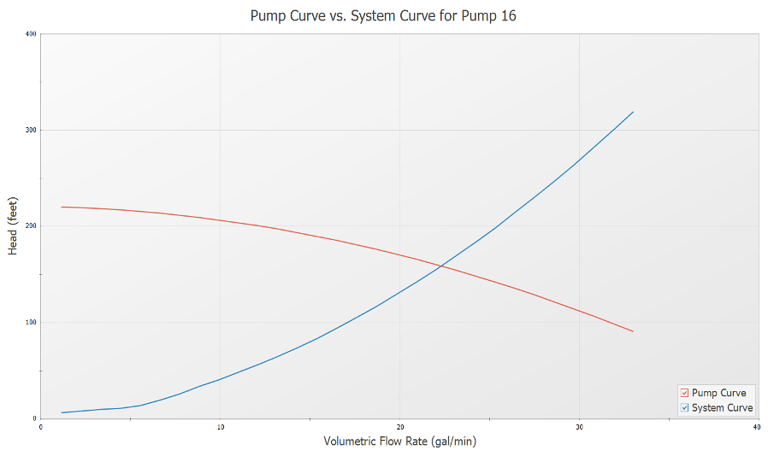
These pumps are made in several impeller configurations to handle a broad range of fluids and materials. Those varieties are:
- Open: Medium efficiency, used for sewage, slurries & light solids handling
- Closed: High efficiency, for water & other thin fluids with no suspended solids
- Semi-Open: Medium-high efficiency, good mixture of the characteristics of open & closed impellers, used for lighter slurries and other general purposes
- Recessed: Low efficiency, for extreme solids handling & heavy sewage/wastewater
- Disc Flow: Extremely low efficiency, for low shear, low flow applications
- Barske Wheel: Low efficiency, used for low-flow, high-head applications such as boiler feed or other regen turbine applications
The rest of the pump can be configured in a nearly endless variety of styles. We highly recommend looking up the different configurations covered in API-610 as a good place to start.
To broadly cover what is available, centrifugals can be broken into these categories, and this list is not all-inclusive (API designations in parentheses):
- End-suction, vertical discharge (OH1 & OH2): The most common pump in the world, used everywhere on everything. Available in nearly any size, material, & seal configuration.
- Self-Priming End Suction (N/A): A subset of standard end-suction pumps, these pumps are capable of pulling a suction lift of 10’-14’ depending on the system & fluid. Found on smaller sump applications and very popular for truck & railcar off-loading.
- Vertical In-line, Overhung (OH3): Highly compact, used in similar applications to end-suction pumps, but where space is at a premium.
- Vertical In-Line, Integrally Geared (OH5 & OH6): High-speed pumps, typically found in boiler feed or other high-pressure booster applications. Used in similar applications to BB4 & BB5 pumps, but where space is at a premium.
- Axial Split-Case (BB1 & BB2): Typically used on very large applications, high flow & low to high head depending on the number of stages (impellers) used.
- Multi-stage Horizontals (e.g., Barrel Pumps, Ring-Section Pumps, BB4 & BB5): High-pressure booster pumps good for boiler feed, injection wells and pipeline charge pumps
- Vertical Turbine (VS1 & VS2): Generally used in large sumps or as main intake pumps, also very common in mine dewatering applications. High flow & very high head available, depending upon the number of stages.
- Cantilever & Lineshaft Pumps (VS4 & VS5): Used in similar applications to the vertical turbine, but generally on a smaller scale as these pumps are normally single-stage.
- Submersible (N/A): A highly versatile class of pumps, most often used in sump applications or where portability is needed.
The advantages of centrifugal pumps include:
- Best Cost-to-Performance Ratio compared to any other type of pump
- Wide Range of Choices regarding configuration & material selection
- Wide Ranges of Flows & Pressures (1gpm – 40,000gpm)
- Produced Pressure is Additive, Not Absolute (e.g., Multi-stage Pumps, Booster applications)
- If sized and operated correctly, these pumps are the least maintenance intensive ones to own & operate
Some engineering considerations/drawbacks with centrifugals:
- Correct sizing is critical
- Not suitable for a system with changing duty points/demand without a control system
- Due to the physics of how they create flow, they are not always consistent in delivering a flow at a set point, and are not well-suited to metering applications
- Controllable via speed control with VFDs, but it is not as simple to implement as with a positive displacement pump
- Unable to be dry-run or dead-headed
- Not well suited to liquids above 400cP viscosity
Everything described in this article reflects general rules, and there are exceptions to nearly every rule. Therefore, it’s best to consult the experts before choosing a pumping solution. We’ve seen our share of mistakes and can help you avoid them.
To determine which type of pump or pumping system is best for your application…